Understanding Material Selection in Aerospace Engineering
Material selection in aerospace engineering is a crucial aspect that determines the efficiency, durability, and safety of aircraft. This process involves choosing the most suitable materials based on their properties, such as strength, weight, and resistance to corrosion, to meet the specific demands of aerospace applications.
The importance of Material Selection Criteria in Engineering Design
Selecting the right materials for aerospace engineering is not just about finding the strongest or the lightest material. It involves a comprehensive evaluation based on multiple criteria including mechanical properties, cost, environmental impact, and manufacturability. Understanding these criteria ensures that the chosen materials will perform as expected under varied operating conditions while being economically viable and environmentally sustainable.Selecting the appropriate material for a specific application significantly influences the performance, maintenance, and lifecycle cost of the final product. For example, while aluminium alloys may offer an excellent balance between strength and weight for aircraft structures, composites like carbon fibre reinforced polymers might be more suited for areas requiring superior strength to weight ratios and corrosion resistance.
Material Selection Criteria in engineering design refer to the standards or guidelines used to choose materials for specific applications. These criteria consider factors such as mechanical properties, cost, environmental impact, and manufacturability to ensure the material’s suitability for the intended purpose.
Example: In designing a jet engine, engineers must consider materials that can withstand high temperatures and stresses. Nickel-based superalloys, known for their excellent high-temperature strength and corrosion resistance, are often selected for critical components such as turbine blades.This selection exemplifies how criteria like temperature resistance and mechanical strength guide the choice of materials in engineering projects, ensuring the components perform reliably in the demanding environment of a jet engine.
Materials Selection in Mechanical Design for Aerospace Applications
Materials selection in mechanical design for aerospace applications requires a deep understanding of the relationship between the mechanical properties of materials and the performance requirements of aerospace components. The process involves not only the consideration of traditional materials such as metals and alloys but also advanced composites and polymers that offer unique advantages.For instance, the use of titanium alloys in airframe structures can significantly reduce weight while maintaining the required strength and durability. Similarly, carbon fibre composites are increasingly utilised in aerospace design for their exceptional strength-to-weight ratio, which is critical for improving fuel efficiency and reducing emissions.
Example: The Boeing 787 Dreamliner utilises carbon fibre reinforced plastics for approximately 50% of its primary structure, including the fuselage and wing. This strategic material selection contributes to significant weight savings, enhanced fuel efficiency, and lower maintenance costs, showcasing the critical role of materials selection in aerospace design.
The Material Selection Process in Engineering: A Step-by-Step Guide
The material selection process in engineering is methodical and structured to ensure the optimal material is chosen for each specific application. This process can be broken down into the following steps:
- Identify the Design Requirements: Clearly outline the performance, aesthetic, and operational criteria the material needs to satisfy.
- Screen for Materials: Use the identified criteria to eliminate unsuitable materials.
- Select Candidate Materials: From the remaining options, assess and compare the materials based on detailed analysis and property data.
- Perform Detailed Analysis: Carry out a comprehensive evaluation of the candidate materials, considering factors such as mechanical performance, cost, and environmental impact.
- Make the Final Selection: Choose the material that best meets the requirements, balancing performance, cost, and other factors.
Choosing materials for aerospace engineering is complex and multifaceted, requiring engineers to stay at the forefront of material science. Innovations in materials, such as the development of stronger and lighter metallic alloys, or advances in composite materials and polymers, continuously extend the boundaries of what’s possible in aerospace design. Undertaking a thorough selection process, considering the full lifecycle of the product, including manufacturing, operation, and end-of-life disposal, ensures not only the performance and safety of aerospace vehicles but also their environmental sustainability. This highlights the evolving nature of materials science and the critical impact of material selection on the future of aerospace engineering.
Advanced Materials in Aerospace Engineering
In aerospace engineering, the quest for higher performance, increased safety, and cost efficiencies drives the continuous evolution and application of advanced materials. These materials must endure the extreme conditions of aerospace environments, including high velocities, temperatures, and pressures, while minimising weight to maximise fuel efficiency.
Selective Laser Melting Materials: Revolutionising Aerospace Manufacturing
Selective Laser Melting (SLM) represents a groundbreaking manufacturing process in aerospace, allowing for the creation of complex, high-strength components directly from digital models. This process uses high-power lasers to fuse fine metal powders layer-by-layer, producing parts that are often lighter and more durable than those created through traditional manufacturing techniques.The choice of material in SLM is critical, as it directly influences the part’s mechanical properties, such as tensile strength, ductility, and corrosion resistance. Today, materials like titanium alloys, nickel-based superalloys, and aluminium alloys are commonly used in SLM processes for aerospace applications due to their optimal combination of weight, strength, and resistance to environmental factors.
Example: Titanium alloys are favoured in SLM processes for producing aerospace components like brackets and housings. These materials offer excellent strength-to-weight ratio and corrosion resistance, critical for aerospace parts enduring high stresses and harsh environmental conditions.
Selective Laser Melting (SLM): A 3D printing or additive manufacturing process that uses a high-power laser to fuse fine metal powders into a solid part based on a digital model.
The Role of Selective Laser Sintering Materials in Modern Aerospace Design
Selective Laser Sintering (SLS) offers another transformative approach to part fabrication in aerospace engineering. Unlike SLM, SLS can utilise a broader range of materials, including polymers, metals, and ceramics, to create complex geometries without the need for supports. The materials used in SLS must exhibit properties that allow them to be sintered into a dense, unified structure while maintaining the desired properties post-processing.Materials such as nylon powders (for their durability and fatigue resistance), aluminium powders (for their lightweight and strength), and glass-filled polymers (for increased stiffness) are prominently featured in SLS applications in aerospace. Their ability to be precisely shaped and customised for specific design requirements makes SLS a preferred choice for prototyping and manufacturing aerospace components.
Selective Laser Sintering (SLS): An additive manufacturing technique that uses a laser to sinter powdered material, binding it together to create a solid structure.
Injection Molding Material Selection Guide for Aerospace Components
Injection molding is a versatile manufacturing process used in aerospace for producing high-volume, intricate components with excellent surface finish. The process involves injecting molten material into a mould to form parts. Material selection for injection molding in aerospace is informed by factors such as thermal stability, mechanical strength, and resistance to chemicals and UV light.Engineered plastics like PEEK (Polyether Ether Ketone) for its high strength-to-weight ratio and resistance to chemicals, and polycarbonates for their durability and transparency, are commonly selected. Furthermore, advanced composites and high-performance polymers are chosen for their unique properties enabling them to withstand the demanding conditions of aerospace applications.
Material | Properties | Applications |
PEEK | High strength, chemical resistance | Aerospace fittings, seals |
Polycarbonates | Durability, transparency | Canopies, windows |
Aluminium Alloys | Lightweight, strong | Structural components |
The evolving landscape of aerospace engineering continuously demands the exploration and integration of novel materials. With advancements in manufacturing techniques like SLM, SLS, and injection molding, engineers can now design and produce components that were once considered impossible. These methods offer unparalleled freedom in design, allowing the creation of parts with complex geometries and tailored mechanical properties, furthering the aerospace industry’s goals of enhanced performance, safety, and sustainability. As material science progresses, the synergy between innovative materials and advanced manufacturing technologies will undeniably shape the future of aerospace engineering.
Challenges and Solutions in Material Selection
Selecting the right materials for engineering projects is essential for ensuring optimal performance, longevity, and sustainability. However, the process involves navigating through a maze of challenges, from the technical constraints of materials to budgetary limitations and environmental considerations. Understanding these challenges and how to overcome them is crucial for engineers and designers alike.
Overcoming Common Obstacles in Materials Selection in Mechanical Design
In mechanical design, the choice of materials plays a pivotal role in determining the functionality and durability of a product. Common obstacles include the availability of materials, their cost and compatibility with other materials, and the complexity of manufacturing processes. Solutions involve:
- Comprehensive database research to evaluate material alternatives.
- Consultation with suppliers to understand the latest advancements and cost-effective options.
- Utilising simulation tools to predict material behaviour and compatibility under real-world conditions.
Material Compatibility refers to the behaviour of different materials when they are used together in a product, focusing on their interactions in various conditions, such as temperature changes or exposure to chemicals.
Example: In aircraft design, aluminium alloys and carbon-fibre reinforced polymers (CFRP) are often used together. However, due to material compatibility issues, such as galvanic corrosion between the carbon fibres and aluminium, engineers need to apply protective coatings or use separators to prevent direct contact, ensuring the longevity and safety of the aircraft structure.
Simulation software not only predicts material performance but also accelerates the development process by reducing the need for physical prototypes.
Material Selection Criteria: Balancing Performance, Cost, and Sustainability
The choice of materials is often a balancing act between performance, cost, and sustainability. Key criteria include:
- Mechanical properties such as strength, durability, and resilience.
- Economic considerations, including material cost, lifecycle costs, and availability.
- Environmental impact, focusing on the material's carbon footprint, recyclability, and ecological footprint.
The process of material selection is increasingly guided by principles of green engineering and sustainability. This includes the preference for materials with low environmental impact, such as those that are recyclable or derived from renewable sources. Additionally, the integration of advanced materials that offer superior performance with minimal ecological repercussions is becoming a paramount concern. Innovations such as bio-based polymers and the development of high-strength, lightweight alloys embody the dual pursuit of excellence in engineering and environmental stewardship. The challenge lies not only in meeting the immediate technical requirements but also in foreseeing the long-term implications of material choices, thus underscoring the need for a holistic approach to material selection.
Future Trends in Material Selection for Aerospace Engineering
The aerospace engineering landscape is constantly evolving, with new materials and technologies paving the way for advancements in aircraft performance, efficiency, and sustainability. The material selection process is critical in developing lighter, stronger, and more resistant components that can withstand the harsh conditions of aerospace environments.
Exploring New Frontiers: Emerging Materials in Aerospace Engineering
Innovations in material science are introducing a wave of emerging materials that have the potential to transform aerospace engineering. These materials are designed to address specific challenges such as weight reduction, thermal management, and environmental sustainability. Notable examples include:
- Advanced composites for improved strength and reduced weight.
- Nanomaterials for enhanced thermal and electrical properties.
- Shape memory alloys for adaptive structures.
Shape Memory Alloys (SMA) are materials that can return to their original shape after being deformed, through a process called shape memory effect. This property is particularly valuable in aerospace for creating adaptive components that can change shape in response to environmental conditions.
Nanomaterials, due to their size, often exhibit properties vastly different from their bulk counterparts, offering innovative solutions for thermal insulation and electrical conductivity.
The exploration of emerging materials is not just about adopting new substances; it's about reimagining the possibilities of aerospace engineering. Advanced composites, for instance, not only offer weight savings but also open up new design paradigms, allowing for more aerodynamic shapes and structures. Similarly, the integration of nanomaterials could revolutionise cockpit electronics, leading to lighter, more efficient, and reliable systems. These trends signify a shift towards materials that don't just meet existing needs but anticipate future challenges and opportunities in aerospace.
How Technological Advancements Influence Material Selection Process in Engineering
Technological advancements play a pivotal role in the material selection process, enabling engineers to optimise designs in ways that were not possible before. Key influences include:
- Digital simulation tools for predicting material behaviour under various conditions.
- Advanced manufacturing techniques like 3D printing for utilising complex materials and structures.
- Material databases and AI-driven tools for streamlining the selection process.
Example: The use of digital twin technology allows engineers to create and test virtual models of aerospace components, simulating real-world performance without the need for physical prototypes. This approach can identify optimal materials and design modifications early in the development process, reducing costs and accelerating innovation.
Artificial Intelligence (AI) in material selection can predict outcomes from complex data sets, offering insights that might not be apparent through traditional analysis methods.
The synergy between material science and technology heralds a new era of aerospace engineering, where the boundaries of what's possible are continually expanded. For instance, the advancement in predictive analytics and AI can lead to the discovery of new material combinations or alloys specifically engineered for aerospace applications, offering unprecedented performance characteristics. Moreover, the advent of advanced manufacturing techniques not only broadens the palette of materials available for use but also revolutionises the way parts are produced, moving towards more sustainable manufacturing practices and innovative design solutions that were once deemed impractical.
Material Selection - Key takeaways
- Material Selection Criteria: Standards or guidelines considering mechanical properties, cost, environmental impact, and manufacturability to ensure material suitability for engineering purposes.
- Materials Selection in Mechanical Design: In aerospace, this involves evaluating the relationship between materials' mechanical properties and aerospace components' performance, including traditional metals and advanced composites.
- Material Selection Process: A structured approach involving - identifying design requirements, screening for materials, selecting candidate materials, performing detailed analysis, and making the final selection.
- Selective Laser Melting (SLM) Materials: Titanium alloys, nickel-based superalloys, and aluminium alloys are used in SLM for aerospace due to their strength, weight, and resistance advantages.
- Selective Laser Sintering (SLS) Materials: Broad range of materials, including nylon, aluminium powders, and glass-filled polymers, used for aerospace applications due to their ability to be sintered into dense structures and maintain desirable properties.
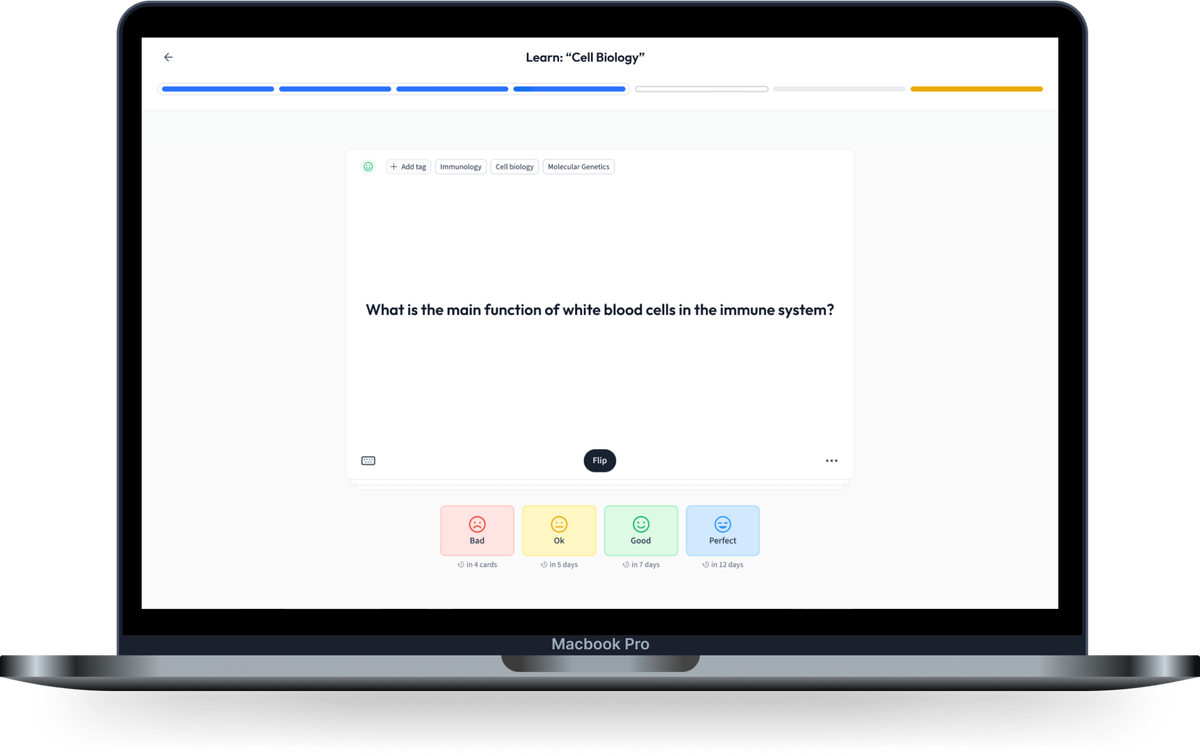
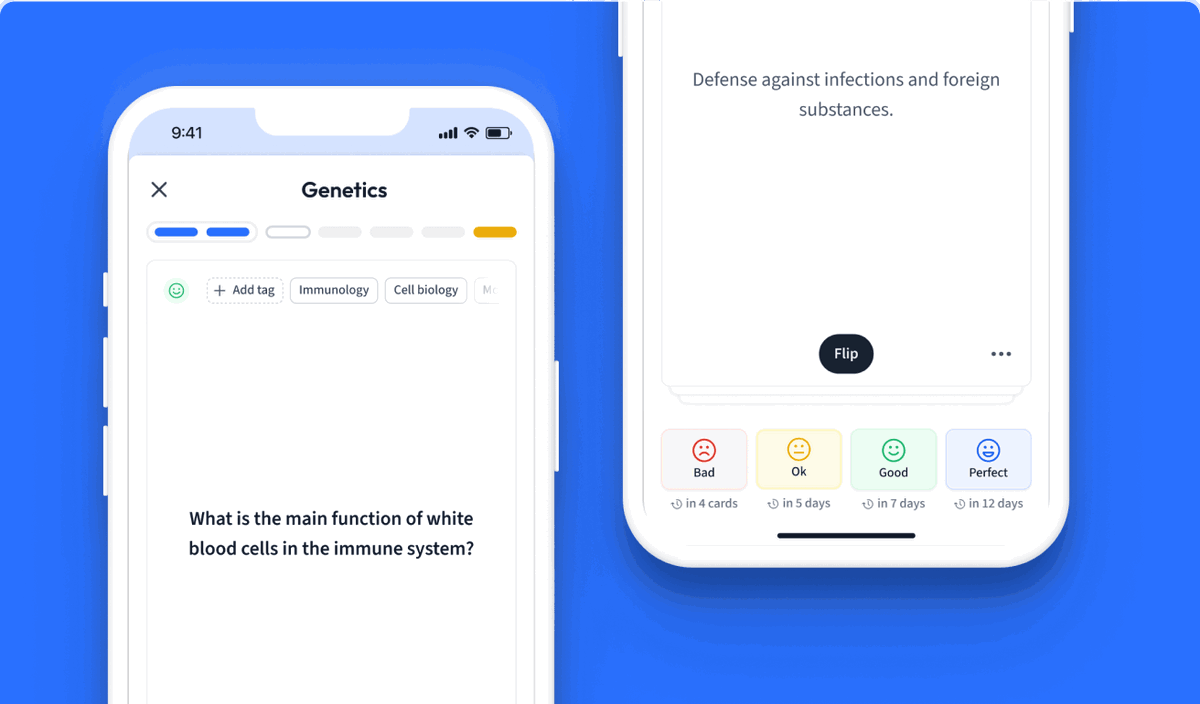
Learn with 12 Material Selection flashcards in the free StudySmarter app
We have 14,000 flashcards about Dynamic Landscapes.
Already have an account? Log in
Frequently Asked Questions about Material Selection
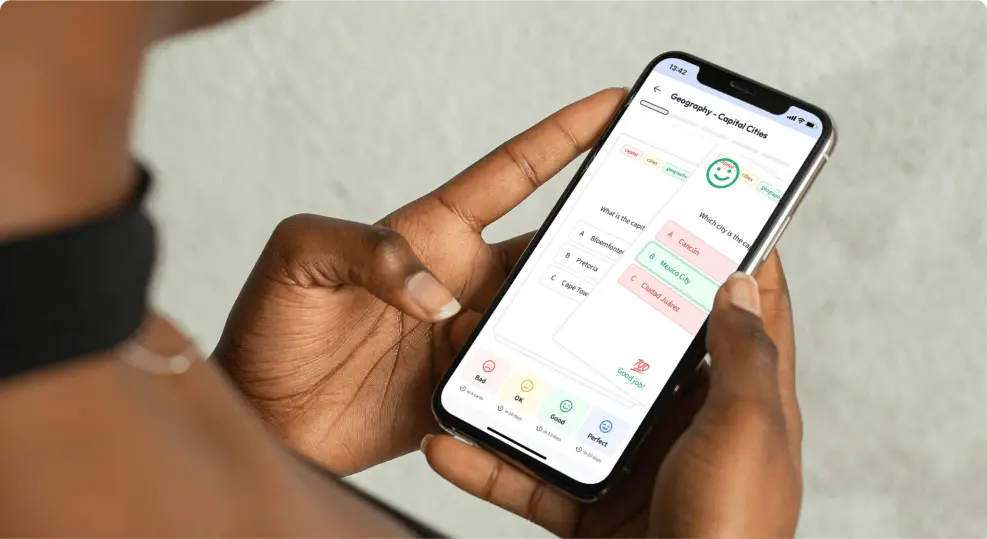
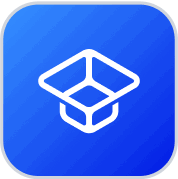
About StudySmarter
StudySmarter is a globally recognized educational technology company, offering a holistic learning platform designed for students of all ages and educational levels. Our platform provides learning support for a wide range of subjects, including STEM, Social Sciences, and Languages and also helps students to successfully master various tests and exams worldwide, such as GCSE, A Level, SAT, ACT, Abitur, and more. We offer an extensive library of learning materials, including interactive flashcards, comprehensive textbook solutions, and detailed explanations. The cutting-edge technology and tools we provide help students create their own learning materials. StudySmarter’s content is not only expert-verified but also regularly updated to ensure accuracy and relevance.
Learn more