Introduction to Prototyping in Design Engineering
As an aspiring engineer, you would have undoubtedly heard about prototyping – an integral step in the engineering design process. The concept of prototyping can be quite fascinating as it involves bridging the gap between an abstract idea and its physical realization. The ability to create a prototype – a working model of a design – empowers engineers to test functionality, demonstrate the concept, and anticipate possible design flaws. To add to that, it also provides a tangible model that engineers can use to communicate their ideas effectively.
Understanding Prototyping - An Essential Tool in Engineering Design
In technical terms, a prototype can be defined as a preliminary model of the final product. The underlying purpose of prototyping is to validate the functionality and feasibility of the design before moving forward to mass production, thereby reducing the risk of failure and the accompanying financial loss.
A prototype, in engineering design, is a working model built to test a design concept by making actual observations and necessary adjustments.
Prototyping paves the path for iterative design; it's a cyclic process of designing, testing, analysing and refining a product or system. The prototyping cycle can be mathematically visualised using the formula:
\[ \text{{Iterations}} = \frac{{\text{{Total Design Time}}}}{{\text{{Time per Design Cycle}}}} \]The ultimate goal is continuously improving precision and efficiency with each iteration, leading to the final successful product.
Let's consider a real-world example of prototyping in action – creation of a new smartphone model. An initial prototype might only represent the physical structure of the phone, showcasing its size, shape, and weight. Once this physical prototype is validated, engineers can conduct simulations to check for mechanical strength, radio signal interference, and other factors. Subsequent prototypes might include a working screen, buttons, camera, and eventually, a fully-functional smartphone for rigorous testing before mass production. This iterative process of prototyping allows for improvements to be made continuously until a model that meets all requirements and specifications is produced.
Diverse Uses of Prototyping in Design Engineering
Prototyping extends far beyond its direct application in product testing and validation. This innovative process benefits various stages of design engineering in numerous ways:
- Customer Engagement: Prototypes offer clear, tangible representations that help customers understand products better and provide valuable feedback.
- Funding and Support: Start-ups often use prototypes to demonstrate the viability of their ideas to attract investors.
- Technical Troubleshooting: Prototyping can help to uncover unexpected technical issues early in the design process.
- Reducing Time-to-Market: Early detection of design flaws through prototyping can accelerate the production process, thereby shortening the product’s time-to-market.
Interestingly, prototyping methods have evolved significantly with technology. Traditional prototyping involves building physical models using materials like wood or metal, whereas contemporary methods entail virtual prototypes created with advanced software tools. Digital prototyping allows engineers to run simulations and analyze performance under various conditions, bypassing the time and cost associated with building physical models. However, physical prototypes still hold their place in validating tactile and aesthetic aspects of a design.
In conclusion, you can now see how key of a role prototyping plays in the world of design engineering. The flexibility and insight it provides during the design process turns ideas into substantial, solid realities.
Methods of Rapid Prototyping
As the name suggests, rapid prototyping pertains to the speedy creation of models utilising three-dimensional computer-aided design (CAD). This technique is well-regarded in the world of design engineering for its ability to materialise complex designs into tangible prototypes with relative ease and efficiency.
What is Rapid Prototyping and its Importance in Design Engineering
Rapid Prototyping (RP) is a group of techniques used to fabricate a scale model of a physical part or assembly using 3D CAD data. Originating from the realm of manufacturing, it plays a crucial role in modern design engineering where speed, efficiency and precision are deemed indispensable. As the pace of industrial innovation accelerates, rapid prototyping has emerged as a powerful tool in navigating the complexities of product development and design troubleshooting.
The power of rapid prototyping lies primarily in its capability to convert complex CAD models into physical 'touch-and-feel' prototypes. This not only enables design verification based on physical models but also helps stimulate creative thought through physical interaction with the prototype. Moreover, rapid prototyping serves as an effective communication tool that can express design ideas more clearly than mere diagrams or verbal descriptions could articulate.
\[ \text{{Importance of RP}} = \text{{Design Verification}} + \text{{Idea Stimulation}} + \text{{Effective Communication}} \]Moreover, rapid prototyping promotes a culture of iterative design. By allowing quick fabrication of design tweaks, the cost and time associated with modifications are drastically reduced. Furthermore, the minimisation of design risks it offers by enabling early detection of design flaws offers substantial economic advantages in the long run.
Various Rapid Prototyping Methods Explained
In light of the diverse needs of design engineering, numerous rapid prototyping methods have been developed. Each of these methods has specialised applications and unique strengths. Here's a quick walkthrough of some of the key techniques:
- Stereolithography (SLA): SLA is an additive manufacturing process that uses a vat of liquid UV-curable photopolymer "resin" and a UV laser to build parts a layer at a time.
- Direct Metal Laser Sintering (DMLS): DMLS is another additive manufacturing process that builds thin layers of metal onto each other to create a fully functional metal component.
- Selective Laser Sintering (SLS): SLS involves the use of a high power laser to fuse small particles of plastic or ceramic powders into a mass that has a desired 3D shape.
- Fused Deposition Modeling (FDM): FDM is a 3D printing technology commonly used for modelling, prototyping, and production applications. It is one of the most flexible and cost-efficient rapid prototyping techniques.
Additive Manufacturing: The process of creating a 3D object by laying down successive layers of material until the object is created. Each of these layers can be seen as a thinly sliced horizontal cross-section of the eventual object.
Strengths and Weaknesses of Different Prototyping Methods
Just as each prototyping method has its unique applications and benefits, they also have their limitations. Understanding these strengths and weaknesses is essential to choose the most suitable method for a particular design project.
Method | Strengths | Weaknesses |
Stereolithography (SLA) | High precision, Smooth surface finish | Material fragility, Limited resin choice |
Direct Metal Laser Sintering (DMLS) | Broad range of metal materials, High detail resolution | High initial investment, Slower build time |
Selective Laser Sintering (SLS) | No need for support structures, Functional plastic parts | Rough surface finish, Limited material variety |
Fused Deposition Modeling (FDM) | Low cost, User-friendly, Variety of materials | Lower dimensional accuracy, Visible layer lines |
As you delve deeper into the world of design engineering and prototyping, these nuanced factors will become guiding principles that inform your choices and help you maximise the effectiveness of your design efforts.
Testing of Prototypes in Engineering Design
Once a prototype is developed, it's time for a critical phase in the engineering design process - the testing. The outcomes of prototype testing largely influence the subsequent stages of product design and development. Testing can yield a wealth of insights, from subtle design flaws to unanticipated end-user difficulties.
Steps Involved in Prototype Testing
The first step on the journey to prototype testing is to define the end goals. Do you wish to evaluate the product's performance under specific conditions, or are you looking to assess how intuitive the design is for the end-user? Identifying the goals beforehand significantly streamlines the testing process and ensures that you obtain valuable, relevant feedback.
Next, develop a well-structured testing plan. This involves selecting suitable testing methodologies and techniques. For instance, you could opt for simulations if you want to assess the design's response to particular stimuli, or you might opt for a focus group if you aim to gauge the product's appeal to a selected demographic.
The third step is to conduct the tests as per the plan. It's crucial to adhere to the pre-decided schedule, ensuring that each test is executed accurately and objectively. Following this, the data collected during testing needs to be thoroughly analysed to draw meaningful conclusions about the performance and feasibility of the design. It's worth noting that testing should ideally be an iterative process — following analysis, the prototype should be refined and re-tested until it meets the predetermined goals.
Finally, the findings must be documented meticulously. This step is vital as the documentation serves to inform future prototype development and final product design.
Importance of Prototype Testing in Design Engineering
Prototype testing occupies a paramount position in design engineering. Not only can it significantly enhance the design's viability, but it can also offer considerable long-term strategic benefits.
Firstly, the primary purpose of prototype testing is risk mitigation. By uncovering design flaws early in the process, you can rectify them at minimal cost both fiscally and temporally. Moreover, the data gathered during testing may afford empirical support for the design decisions, facilitating more confident progression towards the marketing and manufacturing stages.
From a user-centric design perspective, testing provides insights into how the intended users interact with the prototype. It allows engineers to explore and address potential usability issues, enhancing the final product's user-friendliness and, ultimately, its commercial success.
User-Centric Design: An approach to design that grounds the process in information about the people who will use the product. User-centred design processes focus on users through the planner, design, and development of a product.
Lastly, prototype testing can significantly contribute to strengthening customer relationships. By involving end-users in the testing process and incorporating their feedback into the product design, you can foster a sense of ownership and engagement with your potential market.
Common Challenges in Prototype Testing and How to Overcome Them
As decisive as prototype testing may be, it's not without its challenges. However, with a comprehensive understanding of these obstacles, you can devise effective strategies to overcome them.
- Insufficient Testing: One common pitfall is inadequate testing which may stem from budget constraints or strict project timelines. The ideal solution is to prioritise critical tests based on the product's specification and the perceived risks associated with the design.
- Bias in Data Interpretation: Biases in interpreting the test results can skew the design decisions. To overcome this, it's essential to maintain objectivity — paying equal attention to both positive and negative results.
- Unclear Test Objectives: Ambiguity in test objectives often results in irrelevant data collection. This can be avoided by outlining clear, measurable test objectives in the planning stage.
- Unrealistic Test Environments: Tests performed in non-representative environments can yield misleading results. Hence, it is crucial to engineer the test conditions to reflect the anticipated real-world settings as closely as possible.
In summary, though prototype testing presents certain challenges, they can be readily managed with careful planning, clear objectives, and realistic test conditions. As you tread the path of design engineering, honing the ability to build and test effective prototypes will undoubtedly arm you with an invaluable skill set.
Examination of Physical vs Digital Prototypes
In the realm of engineering design, prototyping plays an irreplaceable role in product development. Prototypes exist as tangible embodiments of design ideas, paving the way for testing, evaluating changes, and promoting understanding of a product's functionality. They can be categorised into two broad types - physical and digital prototypes. Each comes with its own set of strengths and restrictions, making them apt for different stages of the design process or different kinds of products.
Overview of Physical and Digital Prototypes in Engineering Design
Physical Prototypes materialise design ideas into concrete models. As actual, tactile representations of the product, they allow designers and stakeholders to observe and interact with the product in the real world. The experience of physically manipulating a prototype offers invaluable insights into attributes like ergonomics, aesthetics, and size, which are challenging to assess digitally.
Physical prototypes can vary greatly in sophistication and detail. Early in the design process, they might be rudimentary mock-ups, created for rapid, iterative testing of broad design features. Later stages might employ high-fidelity physical prototypes, closely replicating the final product's form and function to evaluate performance and user interaction.
A different branch of prototyping brings virtual representations into focus, known as Digital Prototypes. Harnessing digital technology's power, these prototypes exist in software applications, enabling product visualisation and interacting in a simulated environment. This virtual arena is ideal for testing complex systems and interactions that might be costly, time-consuming, or hazardous to replicate physically. Digital prototypes afford designers the liberty to experiment with intricate internal components, simulate extreme conditions, and estimate the product’s response to a variety of stimuli.
Instant modifications, cost-efficiency, and rapid iterative design are further merits of digital prototyping. Via digital models, diverse design variations can be explored without the overheads associated with physical prototyping. Furthermore, with advancements in technologies such as virtual reality (VR), it's becoming increasingly feasible to engage users in immersive digital testing experiences.
Comparing Physical Prototypes with Digital Prototypes
Pros and Cons of Physical vs Digital Prototypes
The determination of which prototyping method to use depends on factors such as the stage of product development, the product type, and the insights you're seeking. A comprehensive comparison can offer valuable guidance in taking this significant decision.
Physical prototypes excel in conveying a realistic sense of the product’s look and feel. They allow stakeholders to explore the product's tangibility and obtain immediate feedback from user interaction. However, they can be expensive and time-consuming, especially when you're working with complex designs. Additionally, repeated alterations, though inherent to prototype development, imply repetitive manual labour, increased costs, and extended timelines.
Physical Prototype Pros:
- Provides a realistic user experience
- Facilitates ergonomic and aesthetic assessment
- Enables user interaction in a realistic environment
- Time-consuming to create and modify
- Can be expensive, particularly for complex designs
- Repetitive manual labour for modifications
Conversely, digital prototypes can simulate complex systems and interactions at a fraction of the cost of physical models. Changes can be swiftly incorporated, and numerous design variants can be examined without substantial expense. However, despite technological advancements, a digital prototype's 'feel' remains incomparable to the actual product's tactile experience. It's also worth bearing in mind that an effective digital prototype requires substantial CAD skills and often, expensive software.
Digital Prototype Pros:
- Cost-efficient for complex systems
- Facilitates rapid iterative design
- Allows simulation under diverse conditions
- Cannot mimic the tactile experience of the actual product
- Requires significant CAD skills and potentially expensive software
The dichotomy between physical and digital prototyping isn't a rigorous one. In practice, the most productive design processes often employ a mix of both types. Early stages might use digital models for quick and cost-effective exploration of design concepts, followed by physical prototypes to validate the design and perform user testing. The application of an apt blend of these techniques, as guided by the design requisites, will culminate in a smooth and successful product development journey.
Guide to Selecting Suitable Prototyping Materials
In the success of an engineering project, the choice of prototyping materials stands as a key component. Whether constructing a physical model or optimising a digital one, selecting an apt material breathes life into the design, representing the nuances of the product's function and properties.
Factors to Consider when Selecting Prototyping Materials
With a vast array of materials available, zeroing in on the perfect one could seem daunting, but the process simplifies by considering a range of factors.
Material Properties: The material you choose should closely mirror the final product's attributes. Consider properties such as strength, durability, flexibility, and resistance to environmental conditions. Be aware of the material's compatibility with the chosen manufacturing process; some substances may not lend themselves well to certain procedures.
Cost: Budget constraints are integral to the selection process. High-quality resources may be desirable, but not always viable given cost considerations. Strike a balance between quality and affordability. Remember, costly materials might prove a drain on resources if lengthy material-consuming iterations are expected.
Product Lifecycle: Consider the development phase: for early stage conceptualisation, inexpensive, easily modifiable materials can help. For client demonstrations or the final design stage, invest in higher quality materials that accurately reflect the intended final product.
Sustainability: With growing emphasis on environmental responsibility, choosing sustainable, recyclable, or less-polluting materials is becoming increasingly relevant in today's design landscape.
Popular Prototyping Materials in Design Engineering
Plastics: A widespread choice for prototyping, plastic offers a range of subtypes, each with unique properties. For example, ABS plastic is renowned for its strength and durability, whereas polypropylene excels for its flexibility and chemical resistance. 3D printing further elevates plastic's utility in prototyping.
Metals: When a prototype requires high strength, durability, or thermal conductivity, metal alloys stand out. Aluminium is often preferred due to its lightweight nature combined with robust mechanical properties. Sophisticated methods like metal 3D printing and CNC machining ensure precise metal prototypes.
Wood: For non-operational mock-ups or spatial models, wood can be a cost-effective, easy-to-work-with choice. Though lacking in versatility when it comes to application in mass production due to its non-homogeneous and anisotropic properties.
Impact of Material Choice on Prototype Performance
The material chosen for a prototype is not just about replicating the physical look of the end product - it can directly influence the model's performance. The choice of material can affect the prototype's functionality, user interaction, and test results, making it an essential determinant in product development.
For instance, selecting a material with insufficient strength or flexibility can lead to structural failures during testing. Even subtle distinctions, such as variances in surface roughness or thermal properties, can significantly influence the findings from a user experience standpoint.
As an example, consider a smartphone prototype. If an inexpensive but brittle material is used, the prototype may crack or shatter during drop tests, giving a false sense of the final product's robustness. Thus, a prototype developed from an inappropriate material leads to unreliable testing results, constraining the scope for design optimization.
The fit between prototyping material and manufacturing process also has notable implications. For instance, using a material inappropriate for a certain machining process may lead to decreased accuracy, wastage, or even damage to the equipment.
In essence, picking the right material for your prototype is very much a design choice in itself and has far-reaching implications on the effectiveness of your prototyping efforts and the efficiency of the overall product design cycle. Understanding the different materials' properties, cost, and suitability to your product requirements and development phase will significantly improve your prototype's performance, and ultimately, the final product's success.
Inspiring Prototype Examples in Design Engineering
While theory and practical guidelines provide indispensable foundations in design engineering, real-world applications often speak volumes about the critical role of prototyping. Here's a glimpse at some inspiring examples of prototyping in design engineering making all the difference.
Exceptional Prototype Examples Explained
Dyson Vacuum Cleaner: The famous Dyson Vacuum Cleaner began as a series of prototypes, over 5000 to be exact. The first few iterations were built out of cardboard, duct tape, and a variety of other accessible materials, setting a classic example of how 'raw' early-stage prototyping can be. Eventually, James Dyson refined his prototype, arriving at the popular 'cyclone technology' vacuum cleaner that revolutionised the industry.
Apple's First iPhone: Apple's pre-eminent stature in the smartphone domain is well-known, but the first iPhone prototype was anything but sleek. It was a clunky device named 'Purple 2', loaded with sensors and ports strictly meant for internal testing. It may seem far removed from today's iPhones, but this prototype was instrumental in gauging suitability and performance before the final design was locked in.
Google's Driverless Car: Google's autonomous driving project, Waymo, began with a prototype named 'Firefly'. Although limited in speed and requiring an attached laptop for processing, Firefly allowed Google to gather valuable data and refine its self-driving algorithms, paving the way for the technologically advanced autonomous giants we see today.
Lessons Learned from Successful Prototype Examples
Success stories from the world of prototyping offer not only inspiration but also key takeaways for budding engineers and designers.
Iterative Development: Both Dyson's vacuum cleaner and Apple's iPhone saw multiple iterations before their final versions. Prototyping lets you take a holistic yet incremental approach towards product development, allowing scope for constant revisions and adjustments in response to testing and feedback.
Courage to Get it 'Wrong': The seemingly 'far from perfect' early prototypes (like the iPhone's Purple 2) embody the courage to fail and learn. Prototyping doesn't require perfection in the first go; instead, it fosters a culture of factoring in and correcting 'missteps', transforming them into strengths over time.
Data-Driven Improvements: Waymo's Firefly is a classic example of leveraging prototyping to gather critical data for improvement. Prototypes provide hands-on, practical evidence about your design's strengths and weaknesses, granting the power to make informed tweaks and changes for enhanced performance.
In essence, these examples of prototyping emphasise an experimental, iterative approach, the willingness to learn from errors, and the capability to leverage data from prototyping to refine the final product. Emulating these principles in your design engineering processes can pave the way for innovative and successful end products.
Deciphering the Meaning of Prototyping in Design Engineering
As you immerse yourself in the world of design engineering, you will come across the term 'prototyping'. But what does it mean? In the simplest terms, prototyping in design engineering can be understood as the process of creating a rudimentary model of a system, often before it is built. It's like a first glimpse into the future project, a vehicle through which the concept comes to life.
Explanation of the Term ‘Prototype’
A prototype is essentially an early sample, model, or release of a product created to test a concept or process. Imagine it as a base working model which offers a practical way to explore ideas and receive feedback before pushing forward to more complicated development stages.
They typically range across scales from very simple, paper-based models to intricate, high-fidelity representations, matching the final product's physical properties and aesthetics, and could even be fully functional. A low-fidelity prototype, for instance, usually has limited interaction and visual resemblance to the final product - it's more a concept demonstration.
On the other hand, a high-fidelity prototype provides a close resemblance to the final product in terms of detail and functionality. It looks and functions as closely as possible to the final design, thereby offering a comprehensive understanding of the end product.
Prototypes serve varying objectives and can, therefore, be categorised differently: proof-of-principle prototypes (confirm basic principles), form study prototypes (investigate dimensions), user experience prototypes (approximate feel and user interaction of final product), and functional prototypes (perform functions of final design).
Role and Significance of Prototyping in Design Engineering
Prototyping forms an integral part of design engineering, striking a balance between theory and practice, and serving as an effective bridge between initial idea and final product. Let's delve into the crucial roles and significance of prototyping in design engineering.
Product Testing: Prototypes offer a practical, hands-on platform to test your product. Rather than just theorising functionalities, you can put your design "to action", checking whether the components function as anticipated, and how the product interacts with the user and the environment.
Testing at the prototyping stage can range from checking individual features, overall user interface, functionality, to other intricate aspects like durability and resilience under diverse conditions. Insights from these tests provide crucial data that drive the adjustments and refinements in future design versions till the end product.
Feedback and Validation: As you progress in the prototyping process, you collect feedback from all possible fronts: internal teams, stakeholders, even potential customers. This feedback is invaluable in shaping the design, pointing out overlooked aspects, bringing fresh perspective, and ensuring that the product is on the right track – meeting user needs and expectations. Thus, the process of prototyping serves as a validation tool, assessing the viability and relevancy of the design early in the development process.
Iterative Improvement: Prototyping encourages an iterative approach to design engineering. What does that mean? In essence, a design is continually modified, refined and tested based on insights and data gathered at each iteration. Essentially, prototypes allow designers and engineers to 'learn by doing' and improve the product gradually until it's ready for launch.
Reducing Time and Costs: While prototyping may require investment in terms of time and resources upfront, its long-term benefits in reducing time and costs are significant. By identifying and rectifying design flaws and issues early in the process before they escalate, the costly revisions at later stages are avoided, and the product-to-market time significantly reduces.
In conclusion, prototyping serves an essential role in design engineering, fostering an environment where creativity and practicality merge. It propels a project forward, providing a clear direction and establishing a tangible foundation from which ideas can be seen, touched, evaluated, and improved upon.
Prototyping - Key takeaways
- Prototype Testing: A critical phase in the engineering design process that influences subsequent stages of product development. Involves defining end goals, developing a testing plan, conducting the tests, analyzing data, refining the prototype, and documenting the findings.
- User-Centric Design: Design process that focuses on the potential users of the product. Prototype testing allows engineers to explore and address potential usability issues, enhancing product's user-friendliness and commercial success.
- Challenges in Prototype Testing: Common issues include inadequate testing, biases in data interpretation, unclear test objectives, and non-representative environments for tests. These can be managed with careful planning, clear objectives, and realistic test conditions.
- Physical vs Digital Prototypes: While physical prototypes offer tangible models for real-world interaction, digital prototypes allow simulation of complex systems and interactions. The choice between the two depends on the stage of product development and the type of product.
- Prototyping Materials: The success of an engineering project is influenced by the choice of prototyping materials, which are selected based on factors such as material properties, cost, product lifecycle, and sustainability. Popular materials include plastics, metals, and wood.
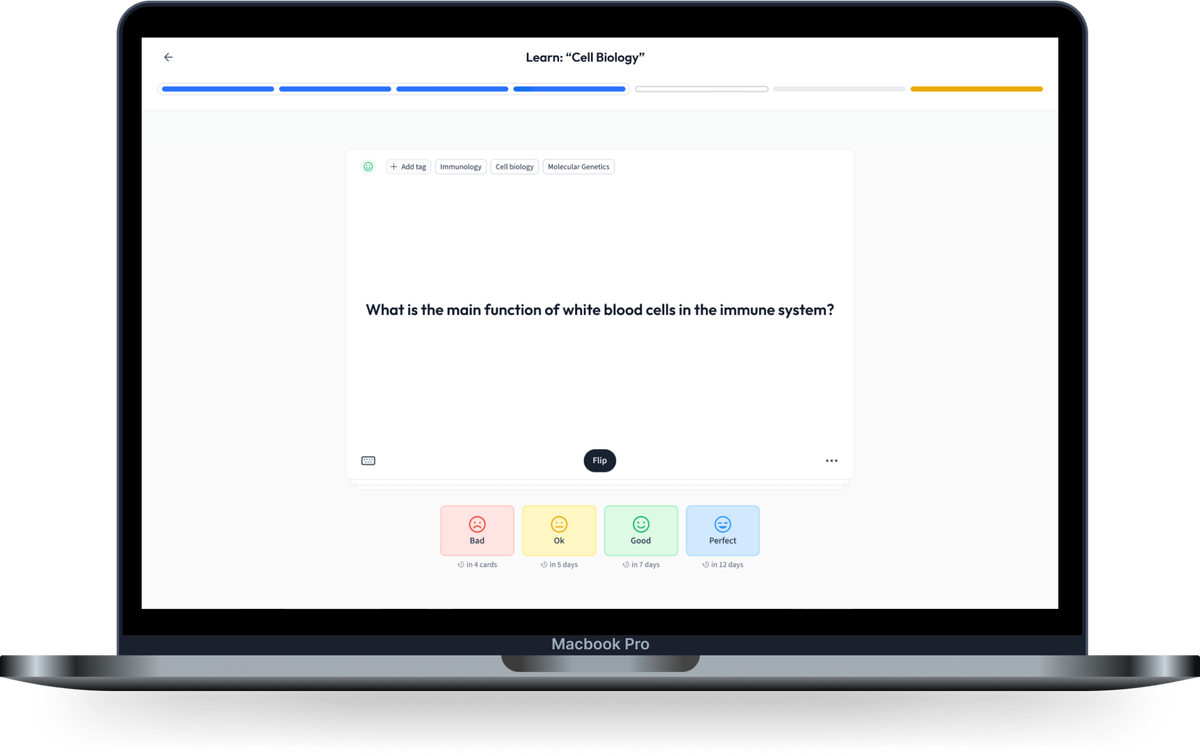
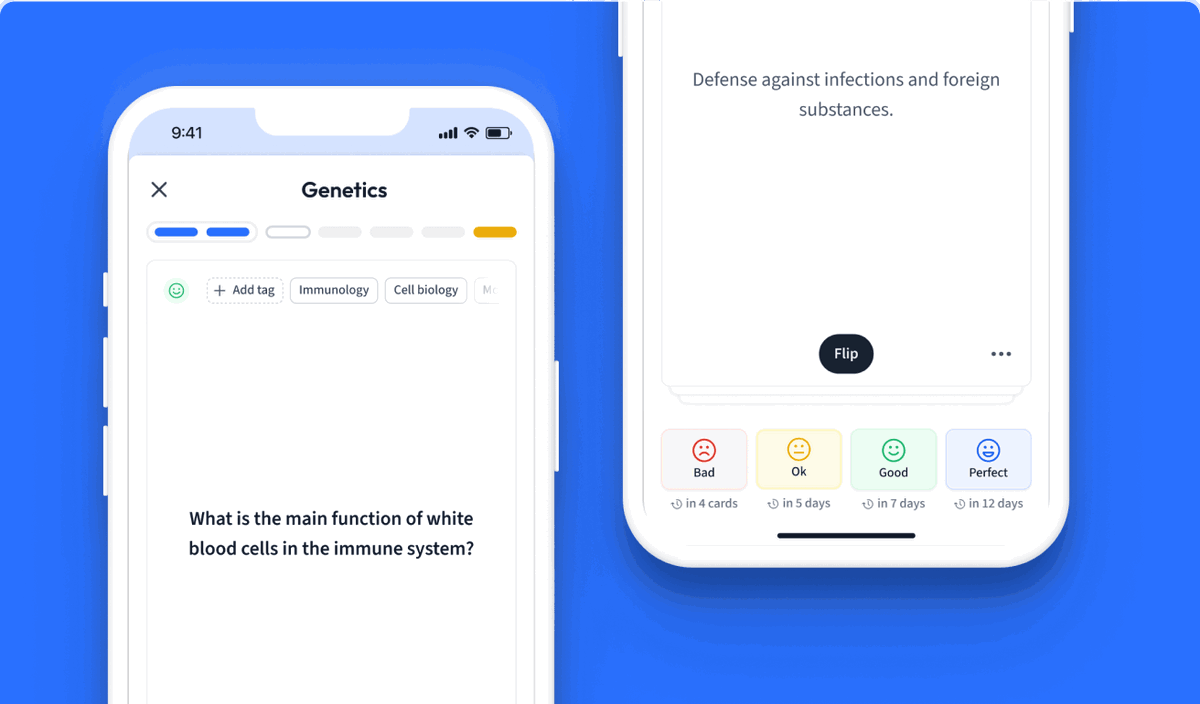
Learn with 14 Prototyping flashcards in the free StudySmarter app
We have 14,000 flashcards about Dynamic Landscapes.
Already have an account? Log in
Frequently Asked Questions about Prototyping
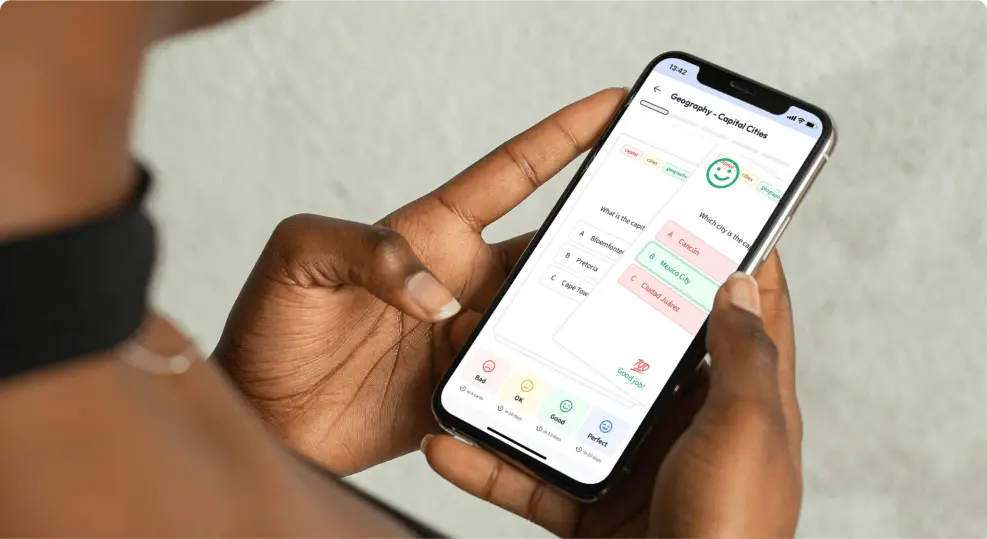
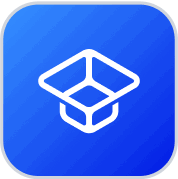
About StudySmarter
StudySmarter is a globally recognized educational technology company, offering a holistic learning platform designed for students of all ages and educational levels. Our platform provides learning support for a wide range of subjects, including STEM, Social Sciences, and Languages and also helps students to successfully master various tests and exams worldwide, such as GCSE, A Level, SAT, ACT, Abitur, and more. We offer an extensive library of learning materials, including interactive flashcards, comprehensive textbook solutions, and detailed explanations. The cutting-edge technology and tools we provide help students create their own learning materials. StudySmarter’s content is not only expert-verified but also regularly updated to ensure accuracy and relevance.
Learn more