- John Ruskin, Philosopher
Quality assurance assists organisations in fulfilling the demands and expectations of clients. An organisation that offers high quality to customers builds trust. This advantage makes the business competitive in the market. If quality assurance is done properly, it will offer confidence and allow the organisation to market their products with less uncertainty. So, what exactly is quality assurance? What are its processes? And what is the difference between quality assurance and quality control?
Quality assurance business definition
Quality assurance (QA) refers to the processes and procedures implemented by a company to ensure that its products or services meet a certain level of quality. The goal of quality assurance is to identify and fix any defects or errors before the products or services are released to the customers.
Quality assurance (QA) can be defined as a set of activities designed to ensure that a product or service meets the specified requirements and quality standards. This involves the establishment of standards and procedures, the monitoring of processes and the implementation of corrective actions when necessary.
Let's take an example of a bakery that wants to maintain consistent quality in its cakes. Quality assurance, in this case, would involve establishing a set of standards and processes to ensure that each cake meets those standards. This may include using specific ingredients, following a recipe, monitoring the baking process, and performing quality checks on the finished product. By implementing these quality assurance measures, the bakery can ensure that each cake meets its desired level of quality, and customers can trust that they will receive a consistently high-quality product every time they visit the bakery.
Quality assurance process
The quality assurance process can be complicated, and the list of steps can be very long. In order to simplify it, we can integrate it with the Plan-Do-Check-Act (PDCA) model, which is a common tool used for the management of continuous process improvement. Here's how stages of the quality assurance process can be mapped to the PDCA model:
Stage 1: Plan
In this first crucial stage, a quality assurance technician or manager will determine clear-cut goals to produce high-quality products and suggest suitable processes to execute those objectives. At this stage, the business can predict any potential problems.
Stage 2: Do
As the name suggests, this stage allows the implementation of the processes identified in the previous phase. The organization carries out its quality plan, which includes establishing procedures, training staff, and implementing quality controls.
Stage 3: Check
In Stage 3, the results of the tests are checked and compared to what was expected. This helps to see if the products meet the required standards. If they do, then the experts move to the final stage. But if they don't, they go back to the first stage to make necessary improvements.
Stage 4: Act/Adjust
In this final stage, the organization takes action to improve the quality plan based on the results of the previous stage. This involves making changes to the quality plan, implementing new procedures, and continuing to monitor the quality results.
Quality assurance methods
QA (Quality Assurance) methods and tools are techniques and instruments utilized to ensure that products and services meet or exceed established quality standards. To commonly used quality assurance methods, we include:
- Identifying processes
- Quality audit
- Control charts
- Benchmarking
- Cause and effect diagrams
Other more advanced tools include six sigma, failure mode and effects analysis, root cause analysis and poka-yoke (error-proofing) method.
Identifying processes
Identifying processes involves defining organizational processes and standards at the beginning of a project to ensure that the development team follows the right path.
Quality audit
Quality audit is a systematic method used to determine how the outlined processes and standards perform during the development and design period. For example, a quality audit might involve reviewing the design documents to ensure that they meet the project requirements.
Control charts
Quality assurance engineers typically use control charts to view process changes and assess whether they are stable in comparison to historical data. These charts can provide a foundation for predicting potential results and ascertaining whether a project should make basic alterations or avoid specific problems. For example, a control chart might be used to track the defect rate for a product over time.
Benchmarking
Benchmarking is a common quality improvement tool that utilizes major performance metrics to find the strengths and weaknesses of procedures. It involves comparing the organization's performance with industry or market standards. Benchmarking can also evaluate prevailing processes in comparison to that of rivals/historic data and hence assist quality assurance experts in recommending suitable actions for improving quality. For example, a company might benchmark its manufacturing processes against those of its competitors to identify areas for improvement.
Cause and effect diagrams
Cause and effect diagrams, also called Fishbone or Ishikawa diagrams, require members to brainstorm and outline all the possible causes of a problem. These diagrams can be useful for identifying root causes of problems and developing solutions. For example, a cause and effect diagram might be used to identify the various factors that contribute to a particular defect in a product.
Internal quality assurance and external quality assurance
Internal quality assurance (IQA) is a process by which an organization ensures that its operations meet quality standards. It involves monitoring and evaluating processes, providing feedback, and implementing improvements in order to maintain and enhance the quality of products or services. IQA is typically carried out by a team within the organization responsible for quality assurance, and it focuses on continuous improvement through feedback and corrective action.
External Quality Assurance (EQA) is a process that ensures consistency, safety, and fairness in assessment and IQA activities carried out by a third party external to the organization. This process is conducted by the Quality Assurer of the Awarding Body.
Quality assurance example
Here are three examples of quality assurance in different industries:
In the manufacturing industry, quality assurance involves inspecting and testing each product during and after production to ensure that it meets the required standards and specifications.
In software development, quality assurance involves testing the software thoroughly to identify any bugs or issues that may impact the functionality or user experience.
In healthcare, quality assurance involves reviewing medical procedures and protocols to ensure that they are safe, effective, and comply with industry standards and regulations. This may include monitoring patient outcomes and conducting regular audits to identify areas for improvement.
The main principles of Toyota’s quality assurance system include ‘customer first’ and ‘quality first'. These principles were formed when the organisation was established. The aim of the quality assurance team is to make sure that each vehicle that comes out of any of their worldwide factories fulfils the organisation’s high standards for safety and quality. There are around 2000 checks performed on every vehicle prior to signing it off as ready for delivery.
Advantages and disadvantages of quality assurance
Quality assurance helps to ensure that products and services meet or exceed customer expectations. While there are various advantages to implementing quality assurance processes, there are also some potential drawbacks to consider. In this regard, below are some advantages and disadvantages of quality assurance that businesses should be aware of.
Advantages of quality assurance
Advantages of quality assurance include:
- Consistent and predictable quality of products or services
- Reduction in defects, waste, and errors
- Increased customer satisfaction and loyalty
- Improved efficiency and productivity
- Identification of areas for process improvement
- Compliance with regulations and standards
Disadvantages of quality assurance
Disadvantages of quality assurance include:
- High initial investment in resources and training
- Time-consuming and complex process
- May create a bureaucratic and rigid system
- Can be difficult to measure the effectiveness of quality assurance
- May not be suitable for all industries or types of projects
- Can lead to a false sense of security and complacency
Quality assurance vs quality control
The main difference between quality assurance and quality control is that QA focuses on developing processes to achieve the expected level of quality and avoid defects, while QC is the process of identifying defects and verifying the quality.
The following table shows the difference between quality assurance and quality control.
Quality assurance (QA) | Quality control (QC) |
|
|
Over time, organisations have acknowledged the importance of quality assurance. Every organisation wants to deliver the best possible high-quality product to its customers. Quality assurance assists organisations in achieving this, thereby facilitating a loyal customer base.
Quality Assurance - Key takeaways
Quality assurance (QA) refers to the processes and procedures implemented by a company to ensure that its products or services meet a certain level of quality.
The goal of quality assurance is to identify and fix any defects or errors before the products or services are released to the customers.
The quality assurance process can be mapped in PDCA model which includes 4 stages: planning, doing, checking, and acting/adjusting.
Quality assurance methods include quality audits, control charts, benchmarking, and cause and effect diagrams.
Quality control is a process by which an organisation makes sure that the quality of the product is maintained or enhanced. It is comprised of testing units, making sure the products are within the range of requirements for the finished product.
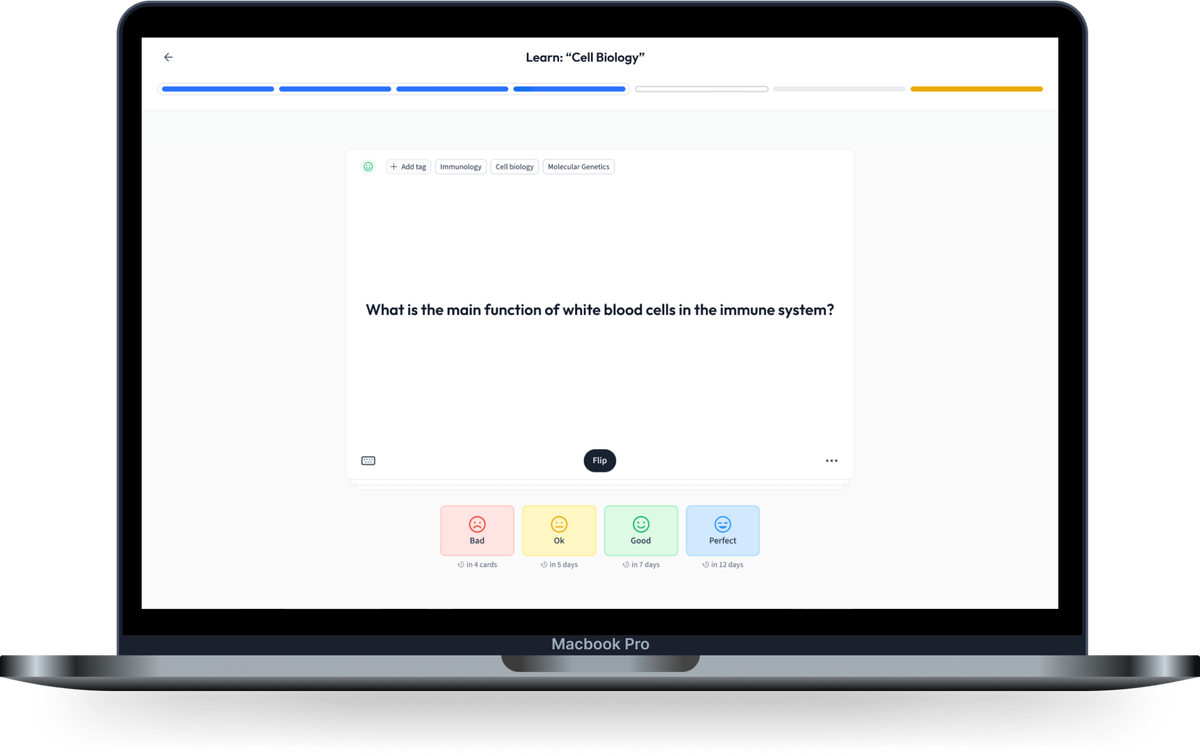
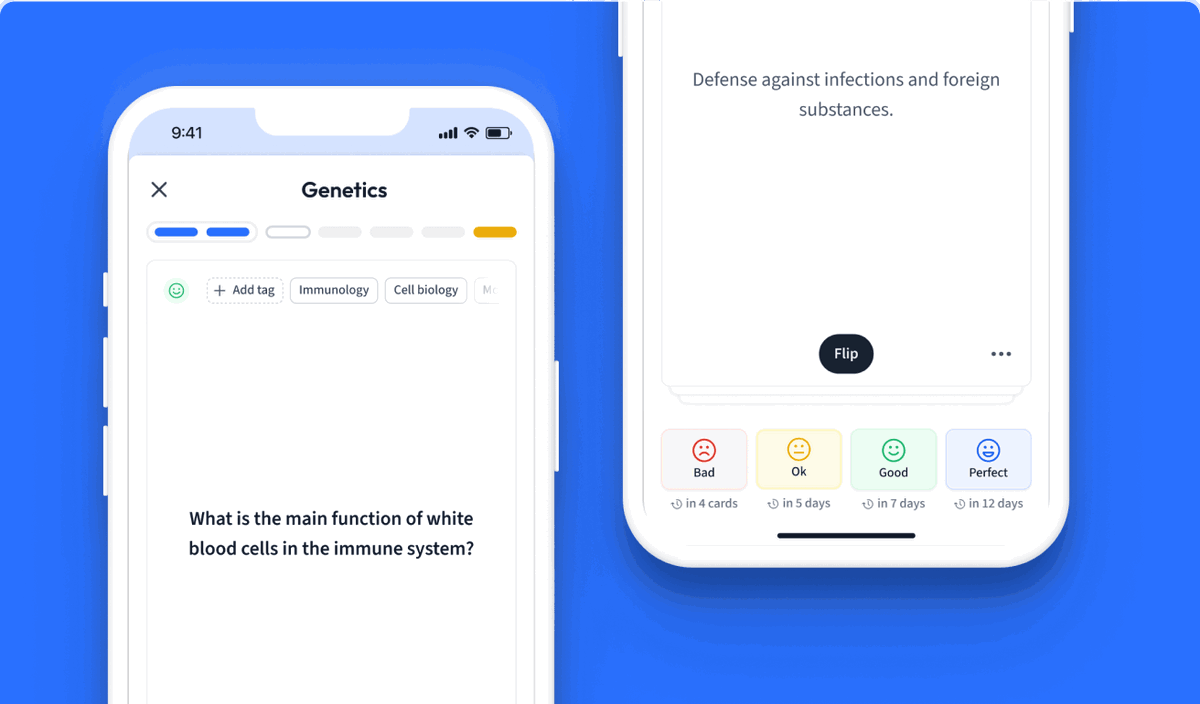
Learn with 106 Quality Assurance flashcards in the free StudySmarter app
We have 14,000 flashcards about Dynamic Landscapes.
Already have an account? Log in
Frequently Asked Questions about Quality Assurance
what is quality assurance?
Quality assurance is any systematic process of making sure that a product/service fulfills the given requirements.
What is the role of quality assurance?
Quality assurance (QA) determines and maintains given specifications for developing and producing reliable products. QA systems are aimed to boost customer confidence and an organisation’s credibility, while enhancing work processes and proficiency, thereby enabling the organisation to better compete with its rivals.
What are the 4 stages in the quality assurance process?
The 4 stages in the quality assurance process are:
Plan, implement, check, and adjust.
What is a quality assurance example?
Comparison of organisation's performance with industry standards.
What is the difference between QA and QC?
QA is process-oriented which means it focuses on the processes related to quality.
and QC is product-oriented which means it focuses on the inspection of products.
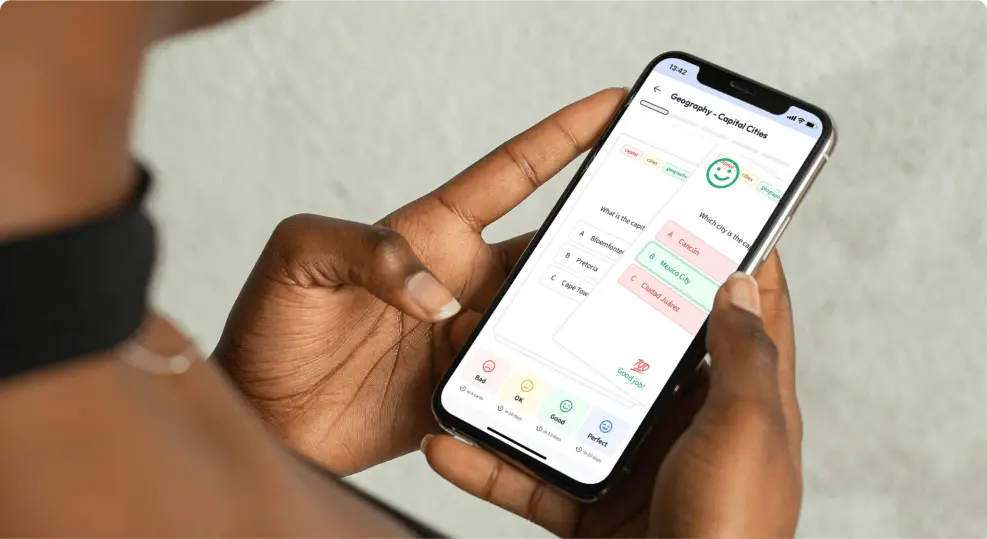
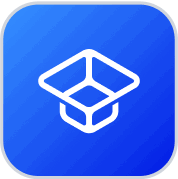
About StudySmarter
StudySmarter is a globally recognized educational technology company, offering a holistic learning platform designed for students of all ages and educational levels. Our platform provides learning support for a wide range of subjects, including STEM, Social Sciences, and Languages and also helps students to successfully master various tests and exams worldwide, such as GCSE, A Level, SAT, ACT, Abitur, and more. We offer an extensive library of learning materials, including interactive flashcards, comprehensive textbook solutions, and detailed explanations. The cutting-edge technology and tools we provide help students create their own learning materials. StudySmarter’s content is not only expert-verified but also regularly updated to ensure accuracy and relevance.
Learn more